Incrementar la Capacidad de Producción Reduciendo Costos Operativos
CCMTY • September 3, 2024
Cómo Incrementar hasta un 30% la Capacidad de Producción Reduciendo Costos Operativos con la Metodología Toyota Way para PYMES
Introducción
La eficiencia operativa es un aspecto crucial para cualquier empresa, pero para las pequeñas y medianas empresas (PYMES), es vital para su supervivencia y crecimiento. En un mercado competitivo, maximizar la capacidad de producción mientras se reducen los costos operativos puede ser la clave para el éxito. Aquí es donde entra en juego la metodología Toyota Way, una estrategia que ha demostrado ser efectiva para grandes empresas y que, con algunas adaptaciones, puede ser igual de beneficiosa para las PYMES. Pero, ¿cómo se puede implementar de manera efectiva sin grandes inversiones en infraestructura o tiempo en capacitaciones? Vamos a descubrirlo.
Entendiendo la Metodología Toyota Way
¿Qué es el Toyota Way?
El Toyota Way es un conjunto de principios y comportamientos que sustentan el enfoque de Toyota para la gestión y producción. Desarrollado por Toyota, esta metodología se centra en la mejora continua y el respeto por las personas, buscando la eficiencia y la eliminación de desperdicios en cada etapa de la producción.
Principios fundamentales del Toyota Way
Mejora continua (Kaizen)
Kaizen, un término japonés que significa "cambio para mejorar" o "mejora continua", es el corazón del Toyota Way. Se basa en la idea de que siempre hay espacio para mejorar, y que las pequeñas mejoras acumulativas pueden tener un impacto significativo a largo plazo.
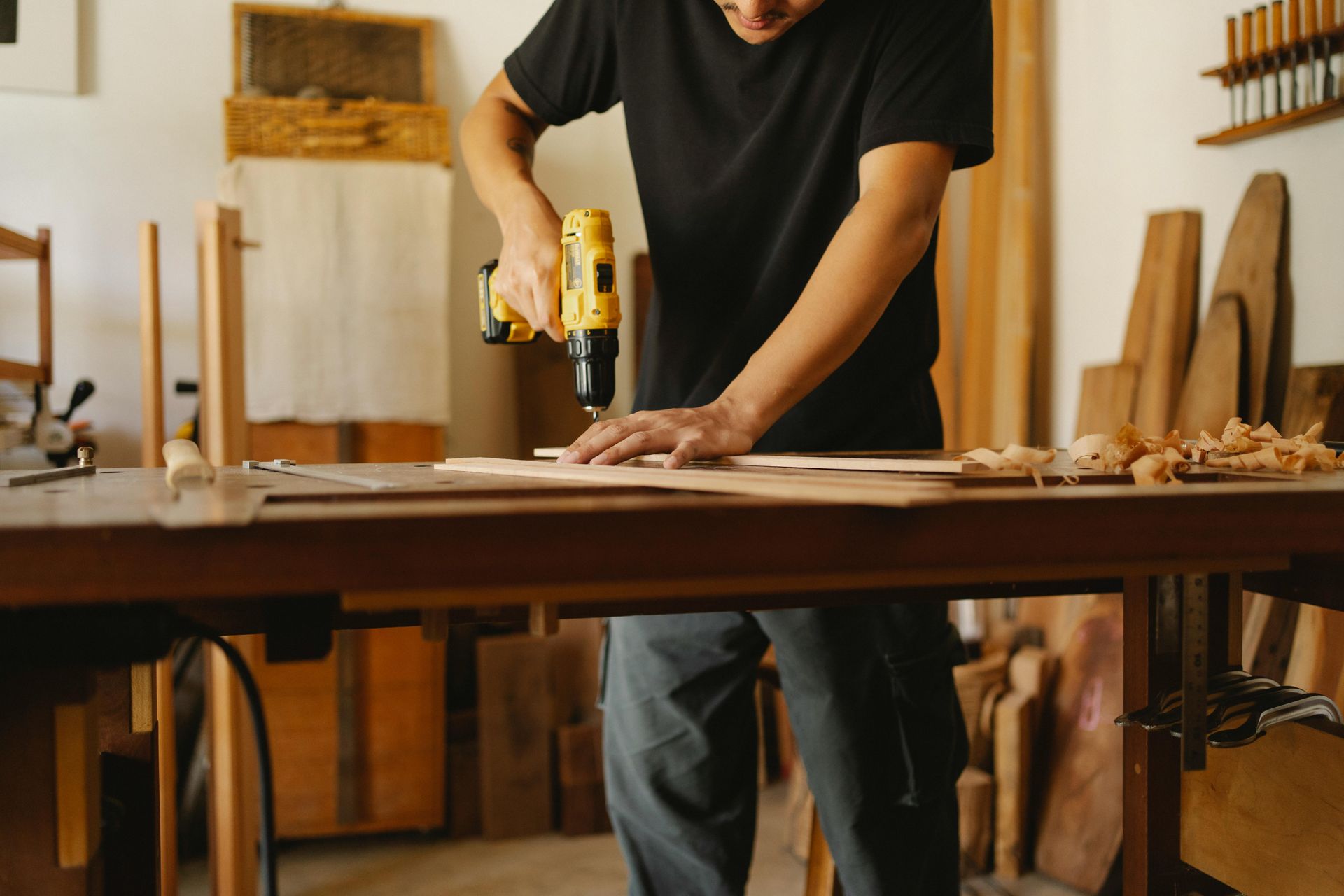
Respeto por las personas
El respeto por las personas es otro pilar fundamental del Toyota Way. Esto implica valorar las contribuciones de cada empleado, promover un ambiente de trabajo positivo, y empoderar a los equipos para que tomen decisiones y contribuyan a la mejora continua.
Aplicando Kaizen para Mejorar la Capacidad de Producción
Identificación de áreas de mejora
El primer paso en la implementación de Kaizen es identificar las áreas donde se puede mejorar. Esto podría incluir la revisión de los procesos actuales, la observación de la producción diaria, y la recopilación de sugerencias de los empleados que están directamente involucrados en las operaciones.
Implementación de pequeñas mejoras constantes
En lugar de hacer cambios grandes y radicales, Kaizen se enfoca en realizar pequeñas mejoras constantes. Por ejemplo, reorganizar el espacio de trabajo para reducir los movimientos innecesarios puede parecer un cambio menor, pero cuando se multiplica por cientos de empleados y turnos, puede llevar a un aumento significativo en la capacidad de producción.
Involucrar a todos los niveles en la mejora continua
Kaizen no es solo responsabilidad de los altos mandos; cada empleado debe estar involucrado en el proceso de mejora. Esto no solo ayuda a identificar áreas de mejora, sino que también fomenta un sentido de propiedad y compromiso entre los empleados.
Enfoque en el Just-In-Time (JIT)
¿Qué es Just-In-Time?
Just-In-Time (JIT) es una estrategia de producción que busca reducir los inventarios y mejorar la eficiencia produciendo solo lo que se necesita, cuando se necesita, y en la cantidad necesaria. Esto minimiza el desperdicio y reduce los costos de almacenamiento y manejo de inventario.
Ventajas de implementar JIT en PYMES
Para las PYMES, la implementación de JIT puede resultar en una reducción significativa de los costos asociados con el inventario y en un aumento en la eficiencia operativa. Al producir solo lo que se va a vender, se evita la acumulación de inventarios innecesarios y se libera capital para otras áreas del negocio.
Ejemplos prácticos de JIT en PYMES
Un ejemplo práctico de JIT en una PYME podría ser la producción bajo pedido, donde los productos solo se fabrican una vez que se ha recibido un pedido, eliminando así el riesgo de sobreproducción y reduciendo los costos de almacenamiento.
Estandarización y Trabajo Estándar
Importancia de estandarizar procesos
La estandarización es clave para asegurar que los procesos se realicen de manera eficiente y consistente. Al estandarizar, se minimizan las variaciones, se reducen los errores, y se asegura que las mejores prácticas se implementen en toda la empresa.
Cómo crear estándares efectivos en una PYME
Para crear estándares efectivos, es crucial documentar los procedimientos actuales, identificar las mejores prácticas, y establecer guías claras que puedan ser seguidas por todos los empleados. Estos estándares deben ser revisados y actualizados regularmente para adaptarse a las mejoras continuas.
Beneficios de la estandarización para la capacidad de producción
La estandarización ayuda a aumentar la capacidad de producción al asegurar que todos los empleados trabajen de manera eficiente y que los procesos sean replicables. Esto también facilita la capacitación de nuevos empleados, reduciendo el tiempo necesario para que se adapten a sus roles.
Cultura de Resolución de Problemas
Introducción al Genchi Genbutsu (Ir y ver)
Genchi Genbutsu, que significa "ir y ver", es un principio del Toyota Way que enfatiza la importancia de ir al lugar donde ocurren los problemas para comprenderlos mejor y encontrar soluciones efectivas. Este enfoque práctico asegura que los problemas se aborden de manera eficiente.
Cómo resolver problemas de forma eficiente
Para resolver problemas de manera eficiente, es importante involucrar a las personas que están directamente relacionadas con el problema. Esto incluye observar de primera mano la situación, analizar los datos disponibles, y colaborar en la búsqueda de soluciones que se puedan implementar rápidamente.
Empoderar a los empleados para tomar decisiones rápidas
El empoderamiento de los empleados para tomar decisiones rápidas es fundamental para mantener la eficiencia operativa. Al darles la autoridad y las herramientas necesarias, se pueden resolver problemas menores antes de que se conviertan en grandes obstáculos para la producción.
Implementación del Sistema Kanban
¿Qué es Kanban y cómo funciona?
Kanban es un sistema visual de gestión del trabajo que ayuda a organizar las tareas de manera que se puedan ver fácilmente las fases en las que se encuentran. Utilizando tarjetas o tableros, Kanban permite a las PYMES gestionar mejor su flujo de trabajo y responder rápidamente a cambios en la demanda.
Ventajas de Kanban en la gestión del flujo de trabajo
Kanban ofrece varias ventajas, incluyendo una mayor transparencia en los procesos, la capacidad de identificar y eliminar cuellos de botella, y la mejora de la colaboración entre los equipos. Esto, a su vez, puede llevar a un aumento en la capacidad de producción y a una reducción en los tiempos de entrega.
Cómo Kanban mejora la capacidad de producción sin costos adicionales
Implementar Kanban no requiere grandes inversiones, ya que se basa en herramientas visuales simples como tableros y tarjetas. A través de una mejor gestión del flujo de trabajo, las PYMES pueden aumentar su capacidad de producción sin incurrir en costos adicionales.
Enfocarse en la Calidad desde la Fuente
Estrategias para prevenir defectos desde el inicio
La prevención de defectos desde el inicio es esencial para mantener la eficiencia operativa y reducir costos. Esto puede lograrse mediante la implementación de controles de calidad en cada etapa de la producción y asegurando que los empleados estén bien capacitados para detectar y corregir problemas en su origen.
Cultura de hacer las cosas bien a la primera
Fomentar una cultura de hacer las cosas bien a la primera no solo reduce el retrabajo y los desperdicios, sino que también mejora la moral del equipo y asegura que los productos finales cumplan con los estándares de calidad esperados.
Impacto en la eficiencia y reducción de costos
Cuando se enfocan en la calidad desde la fuente, las PYMES pueden ver una reducción significativa en los costos asociados con defectos y retrabajos. Además, al minimizar los errores, se mejora la eficiencia operativa, lo que permite aumentar la capacidad de producción.
Implementación del 5S para Mejorar el Ambiente de Trabajo
¿Qué es el 5S?
El 5S es una metodología japonesa que se enfoca en la organización y limpieza del lugar de trabajo para mejorar la eficiencia y productividad. Las cinco fases del 5S son Clasificación, Orden, Limpieza, Estandarización, y Disciplina.
Pasos para implementar el 5S en una PYME
Para implementar el 5S en una PYME, comienza por clasificar y eliminar lo que no es necesario en el área de trabajo. Luego, organiza lo que queda de manera que sea fácil de acceder y usar. Limpia el área regularmente, estandariza estos procesos, y finalmente, mantén la disciplina para asegurar que se sigan las nuevas prácticas.
Beneficios del 5S para la productividad y reducción de costos
Un ambiente de trabajo organizado no solo mejora la moral y la seguridad, sino que también reduce el tiempo perdido buscando herramientas o materiales, lo que incrementa la productividad y reduce los costos operativos.
La Importancia de un Liderazgo Eficaz
El rol del liderazgo en la implementación del Toyota Way
El liderazgo es crucial para el éxito de cualquier iniciativa de mejora continua. Los líderes deben guiar a sus equipos, establecer una visión clara, y asegurar que los principios del Toyota Way se integren en la cultura de la empresa.
Cómo los líderes pueden impulsar la mejora continua
Los líderes pueden impulsar la mejora continua promoviendo una cultura de transparencia y comunicación abierta, proporcionando recursos y apoyo para iniciativas de mejora, y reconociendo y recompensando los logros de sus equipos.
Ejemplos de liderazgo eficaz en PYMES
Un ejemplo de liderazgo eficaz podría ser un gerente que implemente sesiones regulares de revisión de procesos con su equipo, alentando la participación y asegurando que las mejoras identificadas se implementen de manera oportuna.
Monitoreo y Medición del Progreso
Herramientas para monitorear la mejora continua
El uso de herramientas como tableros de control, gráficos de flujo, y software de gestión de proyectos puede ayudar a monitorear el progreso de las mejoras continuas y asegurar que la empresa se mantenga en el camino correcto.
Cómo medir el aumento de la capacidad de producción
Para medir el aumento de la capacidad de producción, es importante establecer métricas claras desde el inicio, como el tiempo de ciclo, la cantidad de unidades producidas por hora, y la reducción en los tiempos de inactividad.
Ajustes basados en datos para mantener la eficiencia
La recolección y análisis de datos permite a las PYMES hacer ajustes informados en sus procesos, asegurando que las mejoras implementadas sean sostenibles y continúen aportando valor a la empresa.
Casos de Éxito de PYMES con la Metodología Toyota Way
Ejemplos reales de PYMES que han implementado Toyota Way
Varios ejemplos de PYMES que han adoptado el Toyota Way muestran que es posible aumentar significativamente la eficiencia y la capacidad de producción sin incurrir en grandes costos. Estas empresas han logrado transformar sus operaciones y mantenerse competitivas en el mercado.
Resultados tangibles en capacidad de producción y reducción de costos
Los resultados incluyen aumentos en la capacidad de producción de hasta un 30%, reducciones en los costos operativos, y mejoras en la calidad del producto, todo gracias a la implementación de la metodología Toyota Way.
¿Cuánto tiempo toma ver resultados con la metodología Toyota Way?
El tiempo para ver resultados puede variar, pero muchas PYMES comienzan a notar mejoras dentro de los primeros meses de implementación, especialmente en áreas como la reducción de desperdicios y la mejora de la eficiencia operativa.
¿Es necesario invertir en tecnología para aplicar Toyota Way?
No necesariamente. Aunque la tecnología puede facilitar algunos procesos, la metodología Toyota Way se puede implementar utilizando herramientas simples y un enfoque en la mejora continua y la optimización de procesos existentes.
¿Qué tipo de capacitación se necesita para implementar Toyota Way?
La capacitación debe enfocarse en los principios fundamentales del Toyota Way, como Kaizen, Just-In-Time, y el sistema Kanban. Es recomendable que la capacitación sea práctica y se realice en el lugar de trabajo para asegurar su relevancia y aplicabilidad.
¿Pueden todas las PYMES aplicar la metodología Toyota Way?
Sí, la metodología Toyota Way es adaptable a cualquier tipo de empresa, independientemente de su tamaño o sector. Lo importante es adaptar los principios a las necesidades específicas de la PYME y asegurar el compromiso de todo el equipo.
¿Cómo empezar a implementar Toyota Way en una PYME pequeña?
El primer paso es identificar áreas clave para la mejora continua y eliminar desperdicios. Luego, puedes comenzar a aplicar pequeñas mejoras utilizando los principios de Kaizen y Just-In-Time, y gradualmente integrar otros aspectos del Toyota Way a medida que se logren resultados positivos.
Programa de Excelenecia mi Pyme
Transforma tu PYME: Descarga Guía con Estrategias Comprobadas para Crecer en 2025
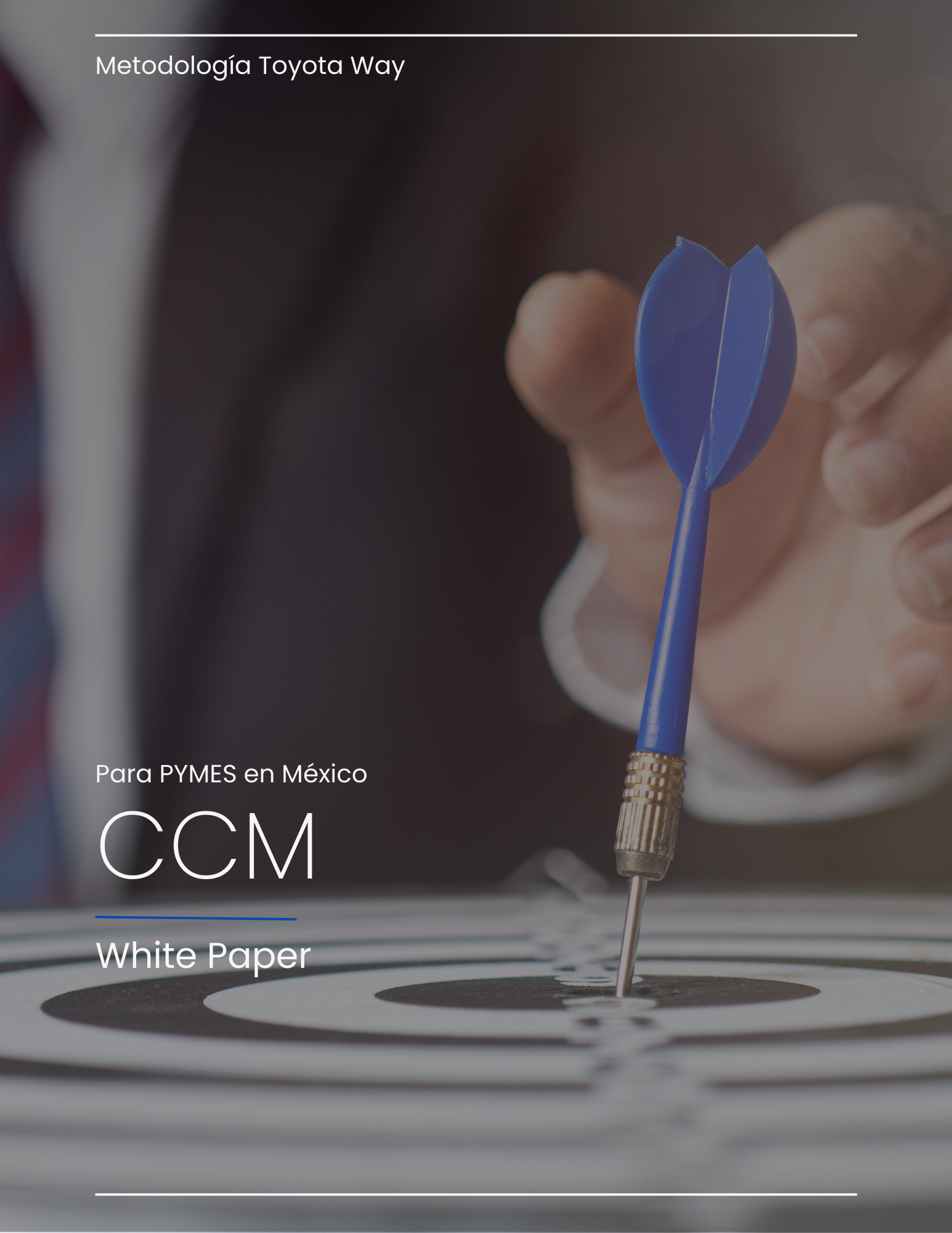